Порошкові наплавочні електроди та стрічки
Нами розроблена та випробувана в промислових умовах ціла гама оригінальних порошкових безвольфрамових наплавочних матеріалів з регульованими властивостями, призначених для зміцнення та реставрації робочих органів обладнання, яке працює в умовах інтенсивного абразивного зношування (див. Фотогалерею №2.1).
Підприємство володіє унікальною технологією зміцнення, яка базується на явищі самопоширюваного високотемпературного синтезу (СВС), зареєстрованого як відкриття у 1985р. Суть цього процесу полягає в локальному ініціюванні реакції зварювальною дугою, внаслідок чого у шихті порошкового електрода виникає хвиля твердофазного горіння з високою температурою, яка поширюється вздовж порошкової суміші з утворенням (синтезом) твердосплавних сполук, котрі переносяться в наплавлений шар, надаючи йому високої твердості та зносостійкості. Таким чином, на відміну від традиційних матеріалів для наплавлення, де тверді хімічні сполуки присутні в готовому вигляді, у матеріалах СВС-класу вони синтезуються в електроді безпосередньо у процесі наплавлення з вихідних компонентів, які вводяться до складу шихти.
Переваги такої технології:
1. Висока твердість і зносостійкість. Наплавочні матеріали СВС-класу, розроблені на базі МНВЦ «Епсілон ЛТД», є мікрокомпозитами, де розмір твердої фази (карбіди та бориди d-перехідних металів) лежать у межах 2-10 мкм і співмірний з розміром частинок абразиву. Це дає змогу даним матеріалам успішно працювати в будь-яких умовах абразивного впливу.
Традиційні наплавлювальні матеріали типу «сормайт» (електроди Т-590, Т-620), які є по суті зносостійкими сплавами, мають ряд суттєвих недоліків, а саме: недостатня твердість (50-60 HRC), невисока зносостійкість, а також значний термічний вплив на поверхню, що наплавляється, та перемішування з основним металом внаслідок концентрації всієї потужності наплавлювальної дуги на стержні електрода.
Електроди СВС-класу дають змогу отримати захисне покриття з твердістю 63-70 HRC, зносостійкість якого при терті по жорсткозакріпленому абразиву в 1,2-1,5 раз перевищує зносостійкість твердих сплавів типу ВК і ацетиленового наплавлення стрічковим релітом (карбідом вольфраму) і в 2,5-3,5 раз зносостійкість електродів типу «сормайт» (див. Порівняльну діаграму зносостійкості матеріалів).
2. Технологічна простота і висока продуктивність. Зміцнення здійснюється методом електродугового наплавлення з використанням серійного зварювального обладнання типу ВДУ, ВДГ і стандартних пристосувань, електродних тримачів і т.п.
Даний наплавочний матеріал можна виготовляти як у вигляді порошкових електродів завдовжки 400 мм для ручного електродугового наплавлення, так і у вигляді стрічки з поперечним перерізом 8х3 мм для механізованих способів наплавлення. Для використання стрічки придатні будь-які моделі серійних зварювально-наплавлювальних автоматів (типу А 1416) після незначної доробки вузла подачі електрода та спеціальні напівавтомати типу “Орбіта-НП”, розроблені на нашому підприємстві.
3. Помірні ціни та доступність. Оскільки при виробництві матеріалів СВС-класу не використовується вольфрам, їхня ціна є співмірною з вартістю традиційних безвольфрамових матеріалів для наплавлення (типу Т-590, Т-620 та пруткового сормайту) і на порядок нижчою від вартості матеріалів на основі карбіду вольфраму, а для реалізації процесу їх нанесення не потрібні жодні додаткові матеріали (кисень, карбід кальцію, захисний газ, флюс і т.п.).
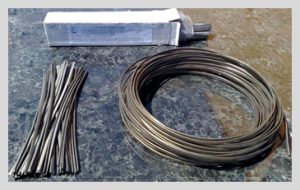
Мал.1 Наплавочні матеріали виробництва ТзОВ МНВЦ “Епсілон ЛТД” (порошкові наплавочні електроди та стрічка)
Для потреб реставрації зношених поверхонь деталей машин з середньою твердістю робочої поверхні 25-40 HRC призначений окремий клас порошкових наплавочних матеріалів. Шар, наплавлений вказаними матеріалами, легко обробляється методом різання, а його товщина не лімітується. Пропонується до застосування при реставрації робочих поверхонь кранових коліс, посадочних поверхонь валів під підшипники та інші робочі елементи, а також елементів великогабаритних зубчатих зачеплень і ланцюгових передач.
Наплавочні матеріали виготовляються в вигляді порошкової стрічки січенням 8х3 мм або порошкових електродів довжиною 400 мм. В залежності від умов експлуатації зміцнених деталей пропонується наступний набір наплавочних матеріалів (див. табл.1).
Ми пропонуємо також розроблення та виготовлення інших типів порошкових наплавочних матеріалів (нержавіючих, жаростійких, з ефектом самозміцнення і т. п.) на замовлення, виходячи з конкретних потреб споживача, виготовлення порошкової стрічки з замовленим хімічним складом наплавленого металу та закатування в металічну оболонку готової шихти сторонніх виробників. Надаємо допомогу в проведенні науково-дослідних робіт з розроблення нових наплавочних матеріалів організаціям та фізичним особам.
Технологія нанесення реалізується шляхом електродугового або плазмового наплавлення в автоматичному, механізованому та ручному режимах з використанням серійного або оригінального наплавочного обладнання з джерелом живлення типу ВДУ-506.
Режими наплавлення приведені в таблиці 2.
Таблиця 1
№ | Марка | Призначення | Характеристики |
Матеріали для зносостійкого наплавлення | |||
1 | Електроди ЕП-ТБ-2-40 тип: 220Т6Р6Х2НС | Зміцнення швидкозношуваних поверхонь деталей, які працюють в умовах інтенсивного абразивного, газо- та гідроабразивного зношування ручним електродуговим способом | Твердість наплавленого шару 63-69 HRC Зносостійкість 3,0-3,5 Коефіцієнт наплавлення 8-8,5 (тут і надалі – г/А год) |
2 | Стрічка СП-ТБ-2-40 тип: 220Т6Р6Х2НС | Зміцнення швидкозношуваних поверхонь деталей, які працюють в умовах інтенсивного абразивного, газо- і гідроабразивного зносу механізованим (автоматичним, напівавтоматичним) електродуговим способом | Твердість наплавленого шару 63-67 HRC Зносостійкість 3,0-3,3 Коефіцієнт наплавлення 14-16 |
3 | Електроди ЕП-ТБ-2-6 тип: 230Т5Р4Х3ГС | Зміцнення швидкозношуваних поверхонь деталей, які працюють в умовах інтенсивного абразивного, газо- та гідроабразивного зносу з помірними ударними навантаженнями ручним електродуговим способом | Твердість наплавленого шару 63-67 HRC Зносостійкість 1,8-2,1 Коефіцієнт наплавлення 8-8,5 |
4 | Стрічка СП-ТБ-2-6 тип: 230Т5Р4Х3ГС | Зміцнення швидкозношуваних поверхонь деталей, які працюють в умовах інтенсивного абразивного, газо- та гідроабразивного зносу з помірними ударними навантаження-ми механізованим (автоматичним, напівавтоматичним) електродуговим способом | Твердість наплавленого шару 62-65 HRC Зносостійкість 1,8-2,0 Коефіцієнт наплавлення 12-14 |
5 | Електроди ЕП-ТБ-1-6 (ЕП-ТБ-1-6.1) тип: 350Х20Г2Т | Зміцнення швидкозношуваних поверхонь деталей (в т. ч. чавунних), які працюють в умовах інтенсивного абразивного, газо-, гідроабразивного та ударноабразивного зносу ручним електродуговим (ацетиленовим) способом | Твердість наплавленого шару 50-55 HRC Зносостійкість 1,4-1,5 Коефіцієнт наплавлення 8-8,5 |
6 | Стрічка СП-ТБ-1-6 тип: 350Х20Г2Т | Зміцнення швидкозношуваних поверхонь деталей, які працюють в умовах інтенсивного абразивного, газо-, гідроабразивного та ударноабразивного зносу механізованим (автоматичним, напівавтоматичним) електродуговим способом | Твердість наплавленого шару 50-53 HRC Зносостійкість 1,4-1,5 Коефіцієнт наплавлення 14-16 |
Матеріали для реставраційного наплавлення чавуну | |||
7 | Електроди ЕП-ТБ-1-11 чавун перлітного класу С – 3,5-4,0% Si – 4,0-4,5% | Наплавлення реставраційного шару, наплавлення шару-підкладки під зносостійку наплавку, заварювання дефектів та заповнення зварних швів (крім кореня) на чавунних деталях ручним електродуговим способом з місцевим підігрівом. Обробляється різанням твердим інструментом | Структура наплавленого матеріалу – перлітний чавун Температура місцевого підігріву 500-680 оС Коефіцієнт наплавлення 8-9 |
8 | Електроди ЕП-ТБ-1-10 модифікований нікелем чавун С – 3,5-4,0% Si – 4,0-4,5% Ni – до 2,5% | Наплавлення реставраційного шару, наплавлення шару-підкладки під зносостійку наплавку, заварювання дефектів та заповнення зварних швів (крім кореня) на чавунних деталях ручним електродуговим способом з місцевим підігрівом. Обробляється різанням твердим інструментом | Структура наплавленого матеріалу – модифікований високоміцний чавун Температура місцевого підігріву 450-500 оС Коефіцієнт наплавлення 8-9 |
* при терті по жорсткозакріпленому абразиву відносно електрода Т-620.
Таблиця 2
Найменування параметру | Значення для електродів | Значення для стрічки |
Полярність дуги | обернена | обернена |
Вольтамперна характеристика дуги | падаюча | жорстка |
Сила струму, А | 180 – 220 | 200 – 450 |
Напруга дуги, В | 30 – 40 | 25 – 35 |
Швидкість подачі електроду, см/с | – | 1,2 – 2,5 |
Швидкість подачі деталі, см/с | – | 0,9 – 1,2 |
Виліт електроду, мм | – | 30 – 50 |
Коефіцієнт наплавлення, г/(А год) | 8,0 – 8,5 | 12 – 16 |
Витрати наплав. матеріалу на 1 дм2 наплавки, кг | 0,24 | 0,20 |
Коефіцієнт використання електроду | 0,93 | – |
Продуктивність наплавлення, дм2 за 1 хв. | до 0,5 | до 1,2 |